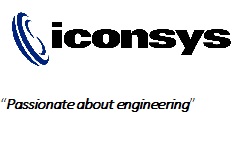
PROJECT OVERVIEW
At a major UK Automotive Customer there is a Painted Body Store (PBS) Plant which provides a buffer between the Plant Paint Shop and Final Assembly. The storage area has capacity for over 600 car bodies. The Plant overall production control system pulls bodies out of the PBS in a fixed sequence for the start of Final Assembly. The project requirement was to upgrade the complete Control System and upgrade mechanically the Conveyor System with new Duplex Chain Conveyors. This Control System Upgrade included replacement of all the PLC, HMI and SCADA systems, replace the Crane, Conveyor and Drop Sections Variable Speed Drive Systems and all the Plant located Op & Control Cubicles, Field Transducers, Safety Systems, Tracking Cameras and communication networks to the latest Control standard as per site and international standards.
The overall system begins with a car body transfer from the Waxing area with a short conveyor section to a drop section which drops the body to 1st floor level. This Drop Section transfers the body to an infeed conveyor system to the PBS area where the body code is read by a Cognex camera prior to storage in the body store (via one of 4 high level cranes over 3 floors) or directly into the fixed sequence as selected by the PBS main controller.
Bodies are removed at the 2nd floor level with another Cognex Camera to read the body code before transfer via a third Drop section lift back to the 1st floor level and then onto the outfeed conveyor to the fixed sequence conveyor.
At the ground floor there is a manual input / output system for maintenance / production control when required.
The infeed from Wax conveyor is 11 off Conveyor Sections and 2 Lift tables. The PBS Input conveyor is 25 off Conveyor sections and 10 off Lift tables. The PBS Output Conveyor is 39 off Conveyor sections and 11 off Lift Tables. The maintenance Input / Output Conveyor is 1 off mobile section and 1 lift table.
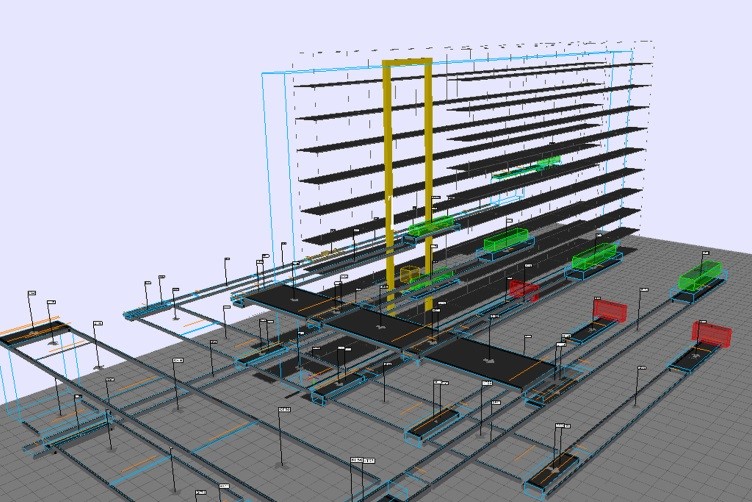
PROJECT OBJECTIVES
To manage the project as Principle Contractor under CDM and to HSE Regulations our scope included engineering, manufacture, installation, obsolete equipment disposal, commissioning over a quick shutdown, training and 24/7 production standby and complete documentation package including Risk Assessment and Safety validation.
The full scope included:- · Replacement new
· Electrical Drive & Control panels
· Field IP67 I/O and motor starters
· Field IP67 Inverters (SEW Movifit)
· Complete new Power & Control Cabling
· SCADA Server and Clients
· HMI Operator Stations
· Safety Light Curtains & Gate Locks
· Feedback sensors
· Cognex Cameras for the input and output conveyor areas
· Cognex Cameras for the PBS cranes
· IR communications to the Cranes
· All duplex chain conveyors & Lift Sections
· Drive coupling mechanics for the Drop Section lifts
· Safety upgrade for the Cranes (PLC / Drives / Optical Comms)
· Interface to:-
· Plant IT systems for storage mapping and production sequencing
· Wax Table upstream PLC via PN-PN coupler
· Fixed Sequence downstream PLC via PN-PN coupler
PROJECT SOLUTION
The overall project comprised of a complex multi drive and control system designed on a Siemens product platform.
The original Store Controller was a Siemens S7-414H, this which was replaced with a new Siemens S7-416F. This PLC communicates to the Plant Production IT systems to manage the body store mapping and select the correct body in the correct sequence for delivery to Assembly. This PLC communicates via Profinet and a high speed InfraRed Link to the 4 off Crane PLC’s (Siemens S7-319F). These high speed cranes insert into and retrieve bodies out from the PBS storage areas.
The main store controller PLC also communicates via ProfiNet to the new Conveyor PLC (Siemens S7-319F) which controls the 81 off conveyor field based Siemens ET200PRO starters, 23 off SEW MoviFit drives and ET200 I/O. All controls and Safety functions are controls via these new Safety PLC’s via ProfiSafe.
New SEW Movidrives (each with quick changeover standby units) for the 2 off Drop sections Lifts using position control via Profinet absolute encoders.
Seven off new Siemens IPC477D HMI’s are installed around the PBS as field Based HMI’s.
Each Crane is fitted with a new Siemens IPC477D HMI for local control.
The main PBS SCADA is based upon one off fault tolerant Server and three off client PC’s running Siemens WinCC software.
The complete system software was tested via WinMod virtual simulation software and bought off by the client prior to commissioning, this significantly reduced risk and meant commissioning could be completed on time.
Much of the PBS’s old safety related parts of the control system did not meet current legislation, so required Risk Assessing and bringing up to the latest PUWER regulations, this part of the upgrade was again provided by ICONSYS including all the necessary validation documentation.
PROJECT FEEDBACK
The project was brought in on time to meet the growing demands of the Plants car production. The new solution is built to the latest Plant standards for both Mechanical and Controls systems requirements
The high quality standards set by Iconsys and the commitment to complete the project to meet the demanding standards of the customer.
Client feedback:
- The new PBS is much better in operation than before.
- When recycling car bodies it now needs just one person to perform this operation. Before it required 3 people.
- Input and Output of bodies is faster than before, reducing bottleneck situations and satisfying the demand from Assembly for bodies. (at full production speed one car is completed every 59 seconds).
- The new system is running well and is much easier to maintain.
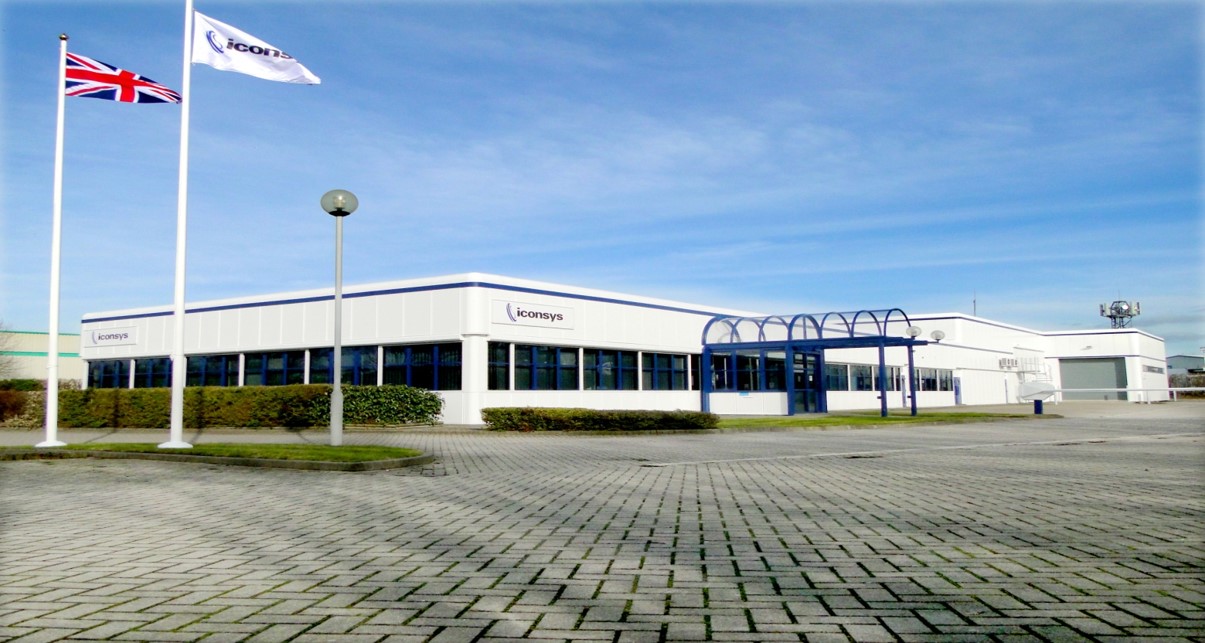