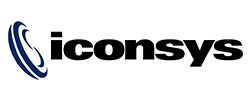
Project Overview
Our material handling customer’s current consumer goods warehouse production process was running at full capacity and with throughput set to increase by an additional 3,000 incoming containers per hour and 2,500 outgoing packages, the customer needed to expand their warehouse operations. The project objective was to install a modern fully automated control system able to cope with current and future demand and in addition, reduce the high level of manual intervention currently experienced at the old warehouse.
The proposed new arrangement planned to incorporate:
· A goods in area, consisting of several infeed lanes, parcel measuring and barcode marking stations
· A fully automated high-volume storage and retrieval system (ASRS)
· 120 operator work stations for value added services
· 2 floors of product storage
· 16 out-loading lanes for packing and despatch for shipping.
· Systems to allow for the re-use and recycling of old cartons, and the dispensing of new cartons
All stock received into the warehouse in containers is scanned and then distributed to the product storage areas, value added services, ASRS or shipping.
A Warehouse Control System (WCS) recognises each individual container and directs the container along its journey. Should there be any holdups or faults an alarm is transmitted to the WCS to enable the container to be reset and sent on its way again.
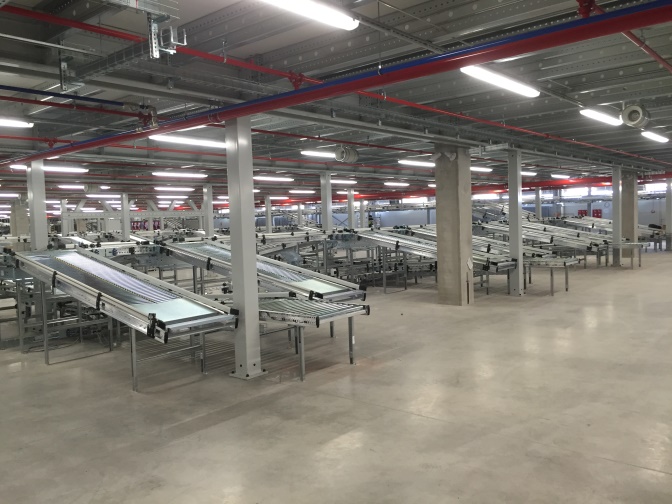
Project Objectives
The planned Automation System needed to include fully distributed controls and monitoring to replace the traditional system of hardwired sensors, actuators and drives currently used at the old site.
All devices were to be controlled over various industrial control networks – ProfiNet, ProfiBus, Ethernet (with ProfiSafe) and ASi. Reducing the wiring and cabling for what would include approximately 100 bar code scanners, 300 emergency stops, 1,000’s of photocells and over 500 motors, together with numerous diverters and 3rd party systems.
Each container has a virtual window of approximately 1 second, so the total time to send an identifying message to the WCS, wait for a response back and initiate a controlling action is critical. The Automation System needed to track containers without further interaction from the WCS on some of the longer conveyor sections.
Automatic label applicators need to be pre-loaded with the information required to generate and apply labels on to moving containers with a positioning accuracy of only a few of millimetres. Weigh scale system would weigh the cartons on the fly and report to the Automation System which would then feed the container details back to the WCS.
Project Solutions
In order to achieve the rates required and handle the volume of communications, 8 PLC (S7-300F series) systems were proposed, including 1 safety system supervisor with distributed safety IO racks using ET200SP. Each PLC is able to communicate directly to its neighbours for efficient transfer of container data from one section to the next.
Industrial Ethernet switches are employed for each PLC. For the industrial networks such as ASi and ProfiBus, repeaters are positioned to improve communication over longer distances.
Instead of wiring motors back to contactors in the PLC or distributed cubicles, power runs were taken to each section of conveyors, and daisy-chained to each field mounted drive / motor group, with a network connection of either ProfiBus or ASi also chained throughout. Group isolation and safety was simplified, and minimal cabling required for runs in excess of 100 meters to many locations. All drives were variable speed and pre-programmed to suit the line requirements.
The Automation System operated a Zenon SCADA system, allowing central monitoring and alarming, for 4 web clients – mobile or remote users. HMIs (Siemens TP-700 Comfort panels) were strategically located together with more than 70 docking stations for hand held Mobile HMIs to give the maintenance crew easy access to all areas of the plant for quick fault-finding.
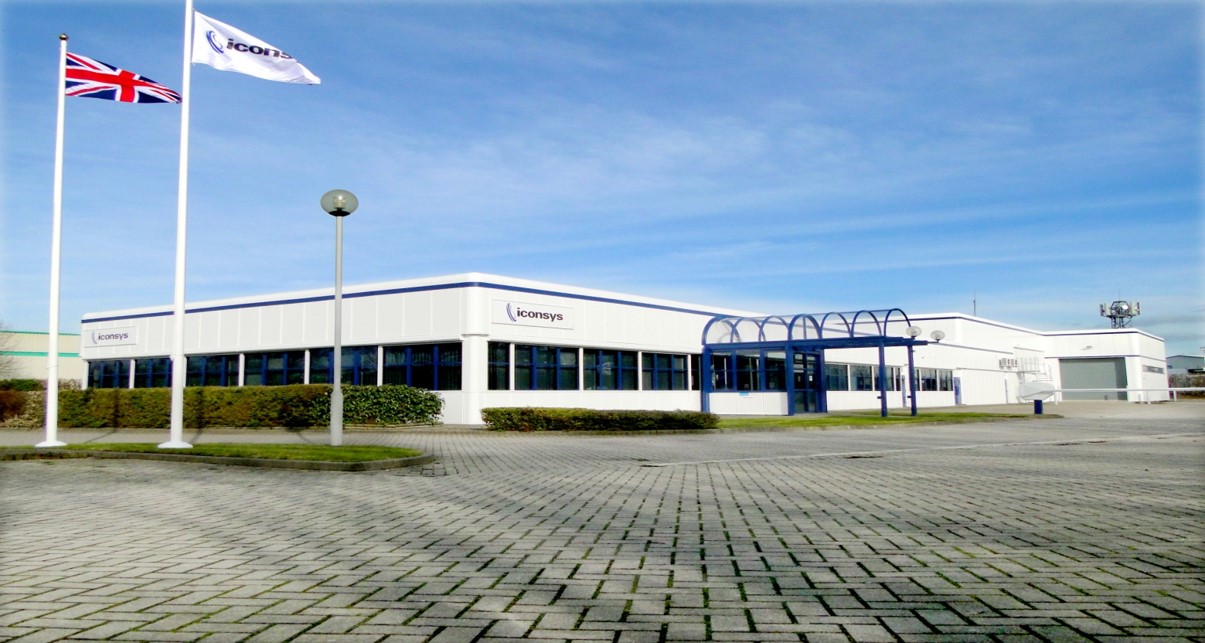