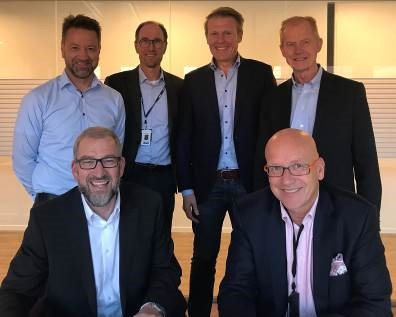
Norwegian retailer expands logistics capacities considerably and acts even more “end-to-end”
Higher capacities and supply chain excellence:
COOP relies on flexibility in processes, throughput, and footprint
The Norwegian food retailer COOP is significantly expanding its central goods distribution center in cooperation with WITRON. Since 2014, the logistics center with a size of 52,000 square meters / 559,700 square feet – located near the Oslo airport – has successfully been supplying more than 1,200 stores throughout Norway with 17,000+ different dry, fresh, and frozen goods. Due to the fact that the automated WITRON warehouse technology has proven to be a distinct competitive advantage for COOP, the expansion is already taking place, only five years after productive start of the system during ongoing operations: From May 2022, COOP will then have a one-third higher order picking volume (a total of 600,000 cases) using WITRON’s solutions OPM, DPS, and CPS on a total area of 84,000 square meters / 904,100 square feet. Thanks to this expansion, COOP will not only achieve a capacity increase, but also a targeted improvement in store and customer service.
In addition to 11 COM machines (then a total of 42), extra automated pallet aisles, tray AS/RS aisles, stacker cranes, and conveyor system components will be installed in all temperature zones. The capacity of the fully automated shipping buffer is also almost doubled. “The existing space will be used for integration and a new building part will be erected”, explains Halvor Nassvik, Senior Project Manager at COOP. “The simple scalability and expandability of the WITRON systems was already an important decision point when we started to design the logistics center”.
Supply chain intelligence from WITRON allows decisions in real-time
Many benefits and use factors were already integrated into the existing solution: error-free order picking, densely packed order pallets, order consolidation, maximum use of trailer space, and ergonomic work processes. Soon will leading-edge functionalities in the WITRON Warehouse Management System provide additional benefits along the supply chain.
“Our distribution center supplies all COOP stores throughout Norway – from large, heavily frequented supermarkets in the city regions down to very small stores in the far north – 2,000 kilometers / 1,200 miles away from the logistics center. Therefore, the supply chain is subject to numerous fluctuations: Purchasing behavior, order quantities, climatic conditions, and routes that our trailers have to cover”, says Roger Nyeng, Logistics Director at COOP. COOP, therefore, requires completely networked processes that react quickly in real-time to changing conditions, to the agility of the market, and to the supply chain.
“If a trailer is stuck in traffic, it must be possible to flexibly change the pick sequence at short notice. If extreme weather conditions are forecasted in the winter and customers tend to stock up, it must be possible to guarantee unplanned order peaks through flexible machine occupation. When the business in the stores calms down during the summer months, the system provides support by means of flexible personnel planning or defines pro-active maintenance cycles”, explains the Logistics Director. “Based on a large amount of data, the WITRON system provides our logistics staff suggestions for actions as to how we can optimally operate the plant in terms of optimized “warehouse intelligence. IT, physics, and processes are, therefore, consolidated in the best possible manner. The seamless integration of other supply chain partners not “only” creates warehouse intelligence, but also a holistic “supply chain intelligence”. Consequently, for COOP this means – in addition to high cost-efficiency – being able to fulfill our customers’ demands even better and in a more sustainable way”.
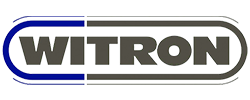