Greater efficiency with Skyfall pouch sorters
Swiss company Ferag AG is installing its highly flexible Skyfall pouch sorters at Blanchisserie Dumoulin, a laundry in the Belgian border town of Comines-Warneton that primarily specializes in laundering hospital linen. Set to go into operation in autumn 2018, the conveyor and sortation system with more than 12,000 pouch is one of the world’s largest in the industrial laundry sector. The system configuration includes five automatic infeed and delivery stations newly developed by Ferag. They ensure a very high level of automation, as well as increasing overall system efficiency. The Skyfall system will handle a daily processing load of more than 20,000 linen sets heat-sealed in plastic film. Each conveyor pouch holds up to seven kilograms.
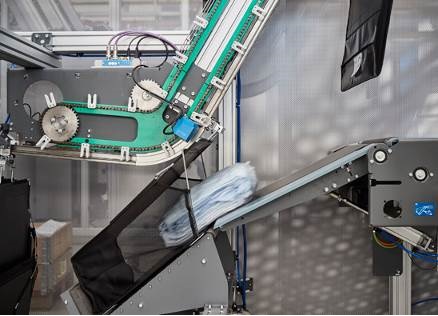
Industrial Laundries - The Trend is Automation
More and more automation is the trend at industrial laundries, especially operations like Dumoulin that increasingly serve healthcare facilities. Among the underlying considerations are hygiene and occupational health: manual contact with the product by laundry staff is to be avoided wherever feasible. On the other hand, the logistical effort required for provision of services only indirectly contributes to value creation, so it is a question of keeping that effort as low as possible. What all this means for the industry is that in addition to automation of the laundering lines themselves, internal material handling and process-related logistics must be largely automated as well.
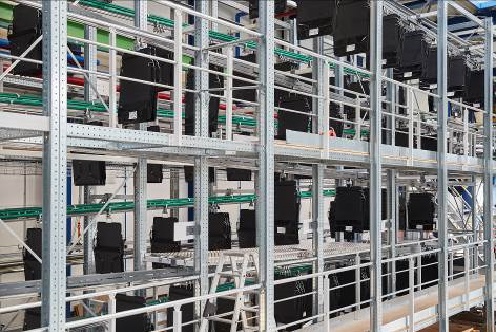
Skyfall Demonstrates its Flexibility
Innovative Skyfall technology, subject to ongoing development by Ferag and tuned for high efficiency, has everything it takes to extend systematic automation in the laundering process to intralogistics processes, too – fast, job-specific sortation as one example. Furthermore, the system demonstrates that this is possible even under the less than ideal conditions of an existing building complex. In a situation like this, the Skyfall overhead conveyor system shows off its full repertoire of space-saving tricks, here packing a 500-metre long circulation conveyor, eight batch lines, a sorter for handling up to 3000 pouches per hour, four 3D buffers with capacity for 3000 pouches each, and an intermediate buffer for 1500 empty pouches into the little room available. Continuing the space-saving theme, the free area under the 3D buffer is able to accommodate five automatic infeed and delivery stations – a further technical highlight of the system currently under construction.
Functionality by Design
Ferag designed the automatic infeed and delivery stations specifically to Dumoulin’s requirements. At the infeed station, laundered and steamed packages of linen freshly heat-sealed in plastic film fall automatically into the pouches. After they pass through various buffering and sortation stages, at the end of the Skyfall line a tilting mechanism tips over the pouches so the items can slide out again. Small rubber flaps and retention flabs ensure that this is extremely easy on products. While each of the stations at Dumoulin will initially handle 600 infeed and delivery operations per hour, in other applications Ferag’s automatic infeed and delivery devices are quite capable of processing up to 2000 units hourly. The 12,000-pouch system still has upward potential that can be brought into play after it has been “run in”.
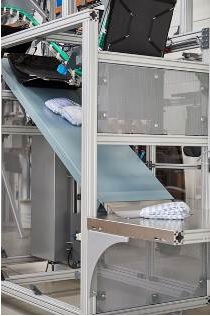
Recognise Clients Values
Blanchisserie Dumoulin, based in Comines-Warneton in the Belgian province of Hainaut, was founded in 1959. The traditional and innovative family-owned business has been run by the second generation since 1992 and enjoys a very good reputation regarding hygienic cleanliness and extraordinary services. As an industrial laundry, it focuses primarily on the healthcare sector as for example retirement and nursing homes as well as hospitals.
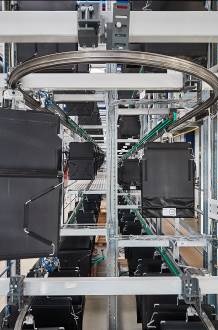