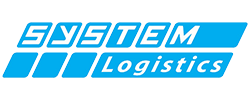
Largerts brewer in Czech Republic and part of Japanese Asahi group turns to AMHSA Member - SYSTEM LOGISTICS as partner.
Plzensky Prazdroj is the largest brewer in the Czech Republic and is part of the Japanese Asahi Group. Since 1842, they have supplied the amber drink to most of Europe, and they were the first brewery to use industrial processes capable of maintaining the fermentation phases unaltered. This manufacturing plant is the major centre of attraction and tourism for the city of Pilsen, where the historic and immense company headquarters are located.
Plzensky Prazdroj had to face the issue of building a new warehouse on land adjoining the production area, optimizing costs and ROI. They turned to System Logistics with the aim of finding a partner capable of tangibly satisfying their needs and guiding them toward the creation not only of a new building, but also of an automated pallet storage system designed to meet their technical and operating specifications. The customer needed to handle 12,000 pallets and initially envisaged a system with stacker cranes.
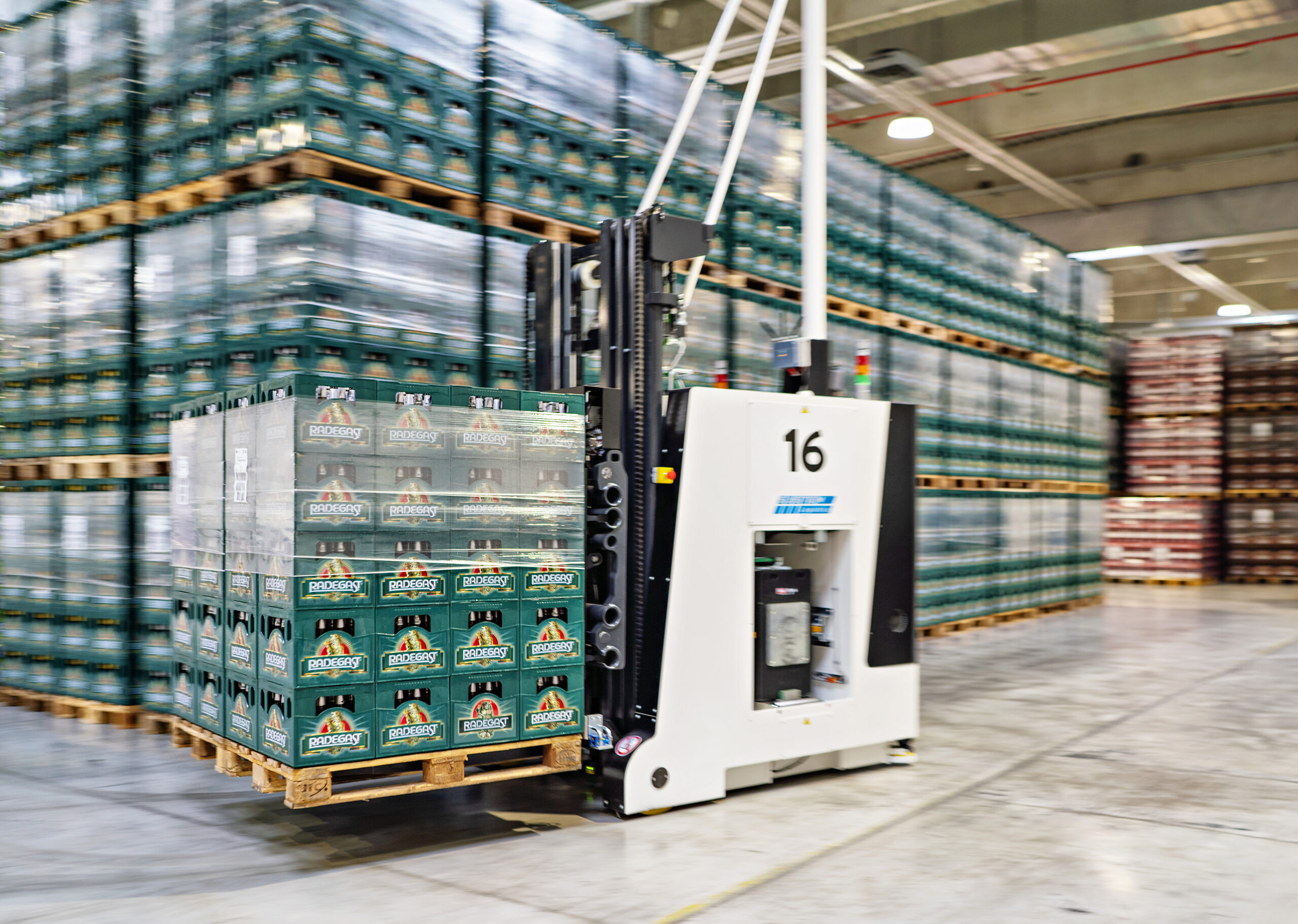
System Logistics’ team analysed all the elements of the project, starting from the construction of the building. In order to achieve the desired result and thanks to a 4-handed work, after evaluating the project development from different points of view, the customer chose a smaller building involving lower construction costs, managed by an automation system consisting of a fleet of 16 AGVs.
The Block Storage (stacked pallets) warehouse is equipped with several areas for sideloading, backloading and secondary distribution, in addition to a dedicated picking area for refilling. The AGV system lifts pallets up to a height of 6 metres and, thanks to the use of single/double forks, it manages all storage and handling operations, including the shelf area dedicated to selective handling of single pallets.
The software system developed by System Logistics is the spearhead of the project: it governs and defines all the required first in first out and last in first out logics, optimizing time and space. This ensured that, despite the complex and ever-changing demands and rules of the end customers, the support operations to picking could be fast and functional. The project began in 2019 in parallel with the construction of the new warehouse floor and became operational in just over 18 months.
“The customer chose us because, in addition to professionalism and competence, they found a reliable work team, ready to listen to their actual needs and willing to work with a proactive, dynamic and collaborative spirit. We implemented an ad hoc project based on our own AGV system and software management. They chose System Logistics’ quality and the value of our people”, commented Mauro Iacconi, senior sales manager, System Logistics.
System Logistics provides innovative intralogistics and material handling solutions for the optimization of the supply chains of warehouses, distribution centres and production centres all over the world. With a focus on the Food & Beverage and Large-Scale Retail sector, System logistics develops customised solutions for automated storage and picking.
The solutions in the range can be used at all temperatures: from ambient temperature, to
controlled or cold temperature (0-4°C) for storing dairy products or fruits and vegetables, to
frozen environments (-25°C).
System Logistics, with headquarters in Fiorano Modenese (MO), has 9 branches worldwide. Since 2016, the company has been member of KRONES Group, international leader in the design, development and production of machines and complete lines for beverage processing, filling and packaging.
For more information, visit www.systemlogistics.com