More flexibility in biscuit baking
An easychain conveyor is now ensuring greater process flexibility and productivity at large-scale Italian confectioner Forno Bonomi in Roverè Veronese in the mountains around Verona. With ten and eleven lines respectively, it is of record size. A chain length of more than three kilometres makes this the biggest-ever 3D plate chain conveyor system from Swiss company Ferag AG. Its several stages form a smoothly functioning bridge between first and second packaging.
The Story, Biscuits - A global demand!
Amarettini, shortbread and sponge finger biscuits along with further varieties are highly popular all over the world, not only with coffee or tea, but also as a small treat between meals. There is a marked trend towards products that have a high recognition value and are based on traditional recipes. This is one of the reasons behind a long-standing boom in fine pastries and confectionery from manufacturers all over Italy. Not least among them is the large-scale confectioner Forno Bonomi, which has a history dating back to 1850 and remains in family hands to this day. The company located in Roverè Veronese, in the Lessinia mountains in the eastern hinterland of Lake Garda, specializes in sponge fingers (Savoiardi), almond biscuits (Mini Amorelli and the like) and – typical of the Verona region – butter biscuits (Tortafrolla di Verona). A very high proportion of these go for export: the fine products of this mid-sized company are present in over 85 countries. Over 65 percent of production output leaves Italy to end up with biscuit connoisseurs in Europe, North and South America as well as Asia.
In view of ever increasing demand, Forno Bonomi was obliged to expand production and adapt it to the requirements of the world market. And so, material handling specialist Ferag was brought on board to implement the conveyor technology required for linking separate production and logistics processes in a project divided into three segments. The readily scalable easychain system was chosen for several reasons. To begin with, when it comes to transfers from first to second packaging, this Swiss plate chain conveyor technology is already established with numerous manufacturers of foodstuffs – the reference list ranges from Gennari to Mondelez to Nestlé. At the same time, easychain technology, easily identifiable with its black and yellow striped plates, offers a number of unique features that were crucially important to Forno Bonomi.
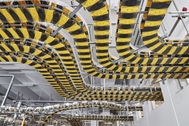
Greater Supply - The Development Need
They start with the conveyor technology specifically developed by Ferag. Its rolling principle is based on components with extremely low kinetic friction; this not only eases motion but also helps the system to operate with only a few drives. Despite the record-breaking chain length of over three kilometres and a total of 20 spirals, just 35 0.75-kW drives suffice to set the conveyor technology in motion throughout the entire plant in Roverè Veronese. The Ferag concept enables an almost maintenance-free system even with high transport throughput. This is due to the easychain conveyor’s supporting plates made solidly out of plastic, supported on robust rollers that run on a pair of sturdy profiled rails that guide them with exceptional quietness and smoothness. This last point is essential for conveyed goods such as biscuits that crumble easily, and makes for particularly gentle transport. Also of great importance: thanks to the rolling principle, the moving easychain parts require no special lubricants, greases or oils. In this respect, the easychain system is predestined for use in the food industry. Furthermore, the rolling nature of an easychain system makes it extremely energy-efficient and that means little electricity is needed. This was another significant aspect for the decision-makers at Forno Bonomi: the company increasingly offers organic products and serves a strongly eco-conscious clientele; thus it attaches great importance to sustainability and environmental compatibility.
But these are by no means all the criteria which led the managers in Roverè Veronese to favour the Swiss system. A further strong argument was that the easychain technology accommodates very tight curve radii. This aspect always comes into play when – as at Forno Bonomi’s main plant – much of the conveyor runs overhead. The associated goal is to gain floorspace for other purposes, such as additional storage or for people to move around. Thus, conveyed goods travel first up and then down again via compact spirals. At the large-scale Italian confectionery plant, ten easychain lines immediately downstream of first packaging take up the cellophane-wrapped biscuits. Immediately following the transfer, a spiral carries the goods upwards through four metres into the mezzanine area of the production hall, which is equipped with ten baking ovens. This terminates the first stage of the conveyor line.
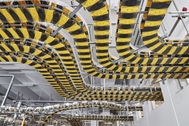
Flexible Solutions
For convenient sorting and rearrangement into new combinations, the owners of Forno Bonomi sought maximum flexibility as well as the ability to swap individual varieties of biscuit on the feeding lines back and forth as required. This is made possible by ten additional easychain lines plus a reserve in the second-stage conveyor. With little effort, a deflector very gently guides selected packages from the feeding lines to the second easychain section, which Forno Bonomi also refers to as the first line.
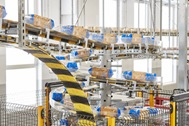
Clever Solutions - An Efficient Interface
Products roll via the first line into the end-of-line area. There they wend their way down from four metres to 90 centimetres above floor level and onwards to one of ten secondary packaging machines, each of which inserts multiple packs into larger cartons. Next step: high-speed pushers specially developed by Ferag quickly yet gently nudge the boxes onto a 200-metre-long easychain circuit that feeds ten palletizing stations. This is where easychain technology comes into its own: as a smoothly functioning conveyor system capable of transporting up to 75 cartons per minute and requiring only three drives for the complete loop, it forms one of the most efficient and flexible interfaces between upstream production and palletizers currently available on the market.
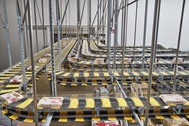