
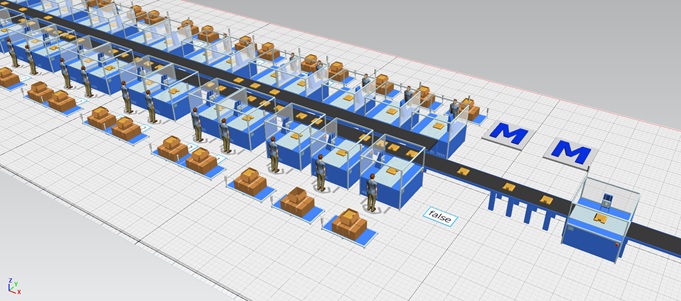
Background
IDC were approached by a leading system integrator to validate a material handling design they were proposing to a customer. Various key points on the system needed to be simulated to ensure that they would perform to the required specification.
Simulation
A full simulation of the proposed system was created using the Siemens Tecnomatix simulation suite. The integrator’s system design layout was transposed into the simulation platform. Data taken from the current semi-manual process was provided by the customer for all aspects of the proposed system. This was then incorporated as a base level for the simulation statistics. Data considered within the simulation included :
· Average number of items per order
· Pack station work rates
· Label application times
· Box creation times per box size
· Operator packing times
· Average % of no-read parcels
· Average % of final orders that required rework
· % downtime of any automation in a given time period
Simulation Experiments
With the simulation modelling the proposed system, IDC were then able to perform a series of test experiments on it. This allows hours of simulated production to run through the simulation platform in a matter of minutes. During this process any points on the system can be set to report back production throughputs, and user key performance indicators(KPI).
IDC then created a matrix of the above user data with multiple variables which meant for example, that different experiments could be exercised at different pack station work rates. In total IDC ran over 100,000 experiments, each one simulating an 8 hour production shift with different variables and work rates.
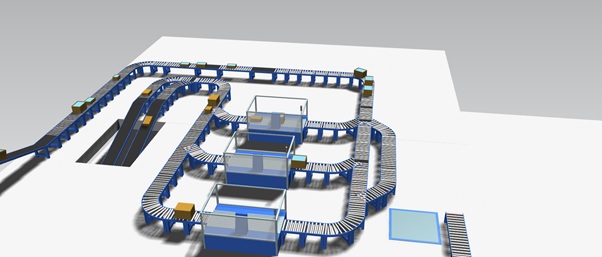
Results
A report was generated that showed the system throughputs for each of the 100,000 experiments, the results could then be ranked and interrogated to show at what point different areas on the system worked at peak efficiency.
Conclusions
The simulation showed that the underlying concept of the proposed system was sound, however certain areas of the design would cause bottle necks that would derail the performance of the whole system unless addressed. This insight gave the system integrator the knowledge to alter parts of their proposal and to gain the confidence that what they were proposing to the customer would meet and exceed the requirements.
The successful simulation is then transferable to the design, build and commissioning phases of the project. This saves on engineering time and reduces the overall project time scale.
If you want to find out how our simulation capabilities could help you with your system design, then please call IDC on 01332 604030 or e-mail